The Art and Science of Personalized Injectable Molding
Custom molding represents a production method which is become vital for the production of complex plastic components across diverse sectors. Such a approach entails injecting molten material into a mold, which it cools and hardens to form the intended shape. The accuracy and effectiveness of custom injection make it a preferred choice for producing high-quality components customized specifically to meet the needs of different uses, ranging from automotive to electronic electronics.
Grasping the art and techniques behind bespoke injection are crucial for companies wanting to improve their production efficiencies. It merges cutting-edge technology and engineering expertise, allowing manufacturers to create detailed designs while maintaining strict tolerances. As industries persist to progress, the need for custom solutions that optimize functionality and affordability increases, making custom molding a crucial method in contemporary production.
Comprehending Injection Molding
The injection molding process constitutes a production method used to create components by injecting heated material into a mold. This approach has been preferred for its capability to produce detailed shapes and significant amounts of uniform high-quality products. A variety of substances, like plastics, metals, and ceramic compounds, can be formed, making it a flexible solution for numerous fields. The procedure begins with the liquefying of the substance, which is then pumped into a sealed form at high pressure.
Once the molten material completes the space of the mold, it hardens and solidifies, assuming the design of the die. The solidification time is determined by the characteristics of the material and the thickness of the part being produced. After cooling, the die releases, and the final component is extracted. This sequence can be repeated quickly, enabling mass production of uniform components. Accuracy and efficiency are key pros of this approach.
Custom injection molding adds an additional layer of difficulty to this method, as it requires designing customized dies designed to meet distinct customer requirements. This means that each die is crafted to achieve the requirements criteria for designs, dimensions, and capabilities. By using custom molds, manufacturers can offer specific products that address the individual needs of various sectors, enhancing innovation and innovation in design development.
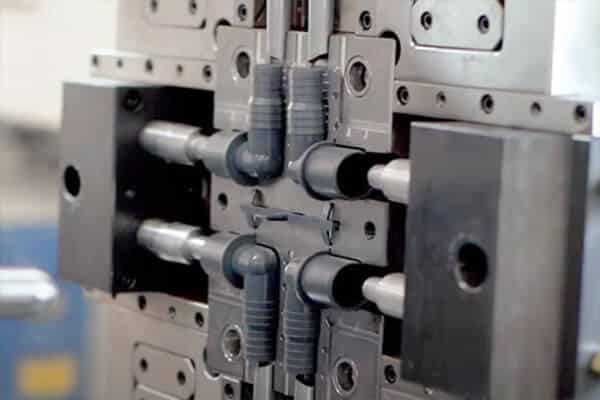
Development Considerations for Tailored Molding
When designing for bespoke injection molding, one of the most crucial elements is the material selection. Various plastics offer various properties such as durability, flexibility, and temperature resistance. The choice of material affects not only the functionality of the final product but also the ease of manufacturing. Designers must work together closely with engineers to ensure the chosen material aligns with the planned application and production needs.
Another essential consideration is part geometry. Complex shapes with detailed details can be difficult to mold, often leading to longer cycle times and increased costs. Designers should aim for simplicity wherever possible, while still retaining functionality and aesthetics. It is also vital to consider the draft angles and tolerances to facilitate the proper release of the part from the mold, which can greatly impact production efficiency.
Additionally, understanding the cooling and heating requirements of the injection molding process is key. Efficient thermal management can help preserve dimensional accuracy and minimize defects in parts. Designers need to consider cooling channels and their location during the mold design stage to optimize the cooling cycle and ensure a reliable quality of the molded parts.
Benefits and Applications
Tailored injection molding provides a variety of advantages that make it an attractive choice for manufacturers across different industries. One of the primary benefits is the ability to produce detailed forms and sophisticated designs with elevated precision. This method allows for tight tolerances, ensuring that each part meets exact specifications. Additionally, the process is extremely efficient, enabling mass production in a comparatively short time frame, which can considerably reduce costs for big orders.
The flexibility of custom injection molding is applicable to a broad range of uses. This technique is frequently used in industries such as automotive, consumer electronics, medical devices, and packaging. Companies can create everything from tiny components to big parts, customizing the materials and finishes to meet the needs of each application. This versatility makes it possible to adapt to changing market demands and utilize cutting-edge materials for improved performance.
Moreover, custom injection molding supports sustainability initiatives. The process can use recycled materials and cut down on waste by removing excess material typically related to other manufacturing methods. This efficiency not only reduces environmental impact but can also produce cost savings for companies seeking to implement green practices. As industries continue to prioritize sustainability, custom injection molding stays a key player in providing forward-thinking and eco-friendly solutions.